Understanding OEM CNC Lathe Machine Parts Factory
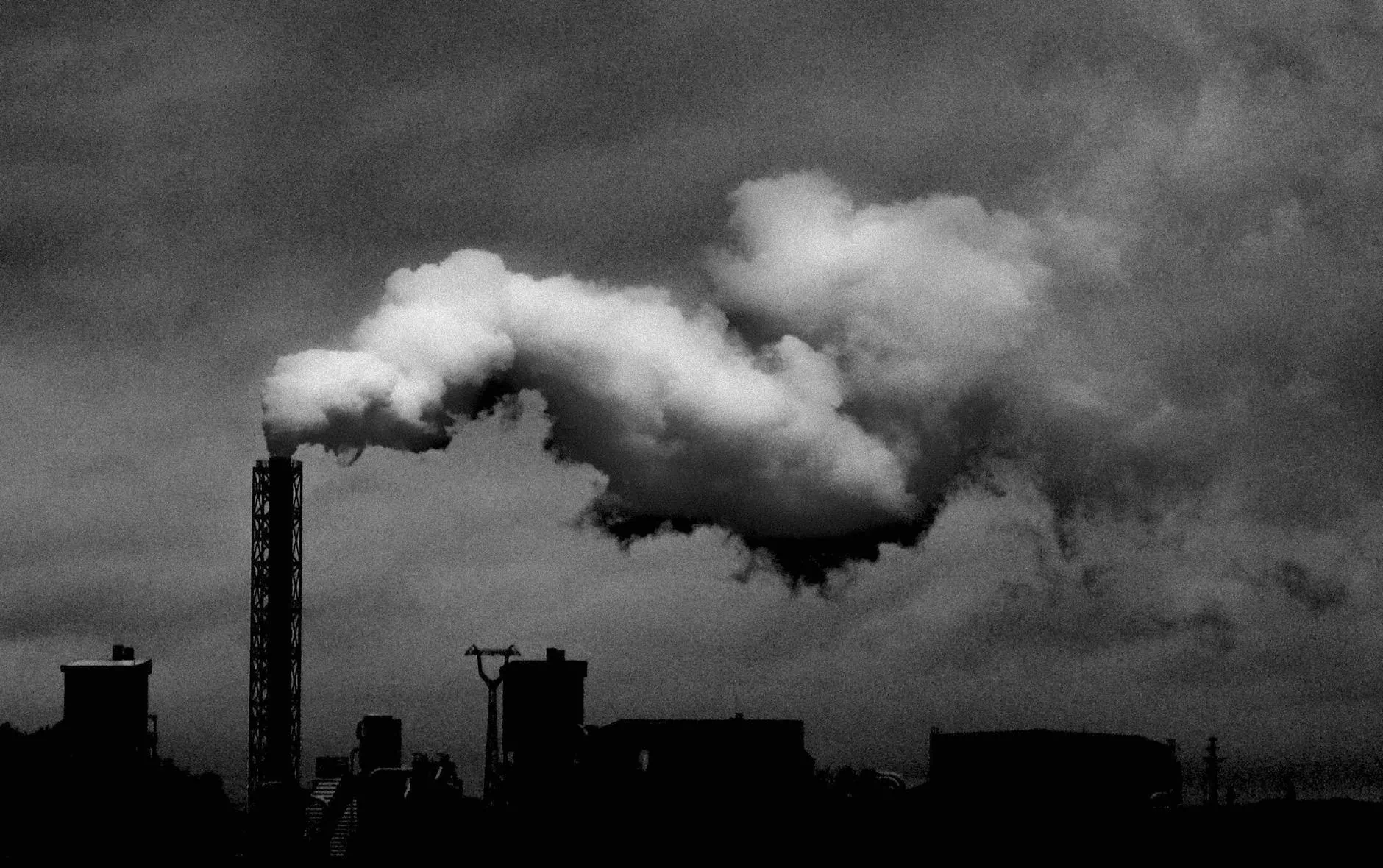
In today’s rapidly evolving manufacturing landscape, the OEM CNC lathe machine parts factory stands out as a critical player. This article delves deep into what defines a successful OEM CNC lathe machine parts factory, the role of metal fabricators, and how quality and precision can significantly impact the industry.
1. What is OEM in CNC Machining?
OEM, or Original Equipment Manufacturer, refers to companies that produce parts and equipment that may be marketed by another manufacturer. In the realm of CNC machining, OEMs are pivotal as they provide the necessary components for various machines, enabling businesses to maintain high levels of production and efficiency.
2. Importance of CNC Lathe Machines
CNC lathe machines are essential in modern manufacturing processes. These machines offer unparalleled precision and consistency, which are crucial for producing high-quality parts in a competitive market. The versatility of CNC lathe machines allows for the manufacturing of a wide array of components, including:
- Automotive parts
- Aerospace components
- Industrial equipment
- Medical devices
- Consumer products
3. The Role of Metal Fabricators in CNC Operations
Metal fabricators play an indispensable role in the manufacturing process. They are responsible for creating the foundational elements of products, which includes cutting, bending, and assembling various metal components. The synergy between metal fabricators and CNC lathe machine operations is vital as it leads to:
- Increased Efficiency: By streamlining the production process.
- High Precision: Ensuring all components fit together seamlessly.
- Cost Savings: Reducing material waste and increasing output.
- Innovation: Enabling the rapid development of new products.
4. Quality Assurance in OEM CNC Lathe Production
Quality assurance is paramount in an OEM CNC lathe machine parts factory. Implementing strict quality control measures ensures that each part meets the specified standards, thus reducing the likelihood of defects. Steps include:
- Incoming Material Inspection: Verifying the quality of raw materials before production.
- Process Control: Monitoring CNC machining processes to maintain precision.
- Final Inspection: Conducting detailed checks on the finished products before shipping.
5. Innovative Technologies in CNC Machining
To stay competitive, an OEM CNC lathe machine parts factory must adopt innovative technologies. These advancements not only enhance production efficiency but also improve product quality. Some notable technologies include:
- Automation: Utilizing robotics to reduce lead times.
- Advanced Software: Implementing CAD/CAM systems for precise programming.
- 3D Printing: Allowing rapid prototyping to test designs before full-scale production.
- IoT Integration: Enabling real-time data tracking and process optimization.
6. Challenges Faced by OEM CNC Lathe Machine Parts Factories
Despite the advancements, OEM CNC lathe machine parts factories face significant challenges:
- Rising Material Costs: The fluctuations in raw material prices can impact production costs.
- Skilled Labor Shortage: The lack of skilled machinists can hinder operational efficiency.
- Technological Upgrades: Keeping pace with rapid technological advances requires substantial investment.
- Global Competition: Competing on a global scale necessitates continuous improvement and innovation.
7. Best Practices for Success in CNC Machining
To thrive in the competitive landscape of CNC machining, an OEM CNC lathe machine parts factory should prioritize best practices. These include:
- Continuous Training: Investing in employee training to enhance skills.
- Regular Maintenance: Ensuring CNC machines are well-maintained to prevent breakdowns.
- Customer Feedback: Utilizing customer feedback to improve product offerings.
- Flexible Workflow: Adapting to changing market demands quickly.
8. The Future of CNC Machining and OEMs
The future of CNC machining and OEM manufacturers looks promising, driven by technological innovation and increasing demand for customized solutions. As industries evolve, the need for more intricate and precise components will rise.
Companies like Deep Mould are at the forefront, ready to leverage new technologies and practices to meet the challenges ahead while ensuring top-notch products for clients. By focusing on quality, efficiency, and innovation, these factories will continue to thrive and lead the market.
Conclusion: Why Choose Deep Mould for Your CNC Needs
In conclusion, the OEM CNC lathe machine parts factory is a vital component of the manufacturing ecosystem. By selecting established fabricators, such as Deep Mould, businesses can ensure that they receive only the highest quality parts that meet and exceed expectations. With a relentless commitment to quality, efficiency, and innovation, Deep Mould is dedicated to being your reliable partner in the world of CNC machining.
Explore more about how we can help you improve your manufacturing processes by visiting Deep Mould today!