The Future of Manufacturing: Silicone Injection Molding Machines
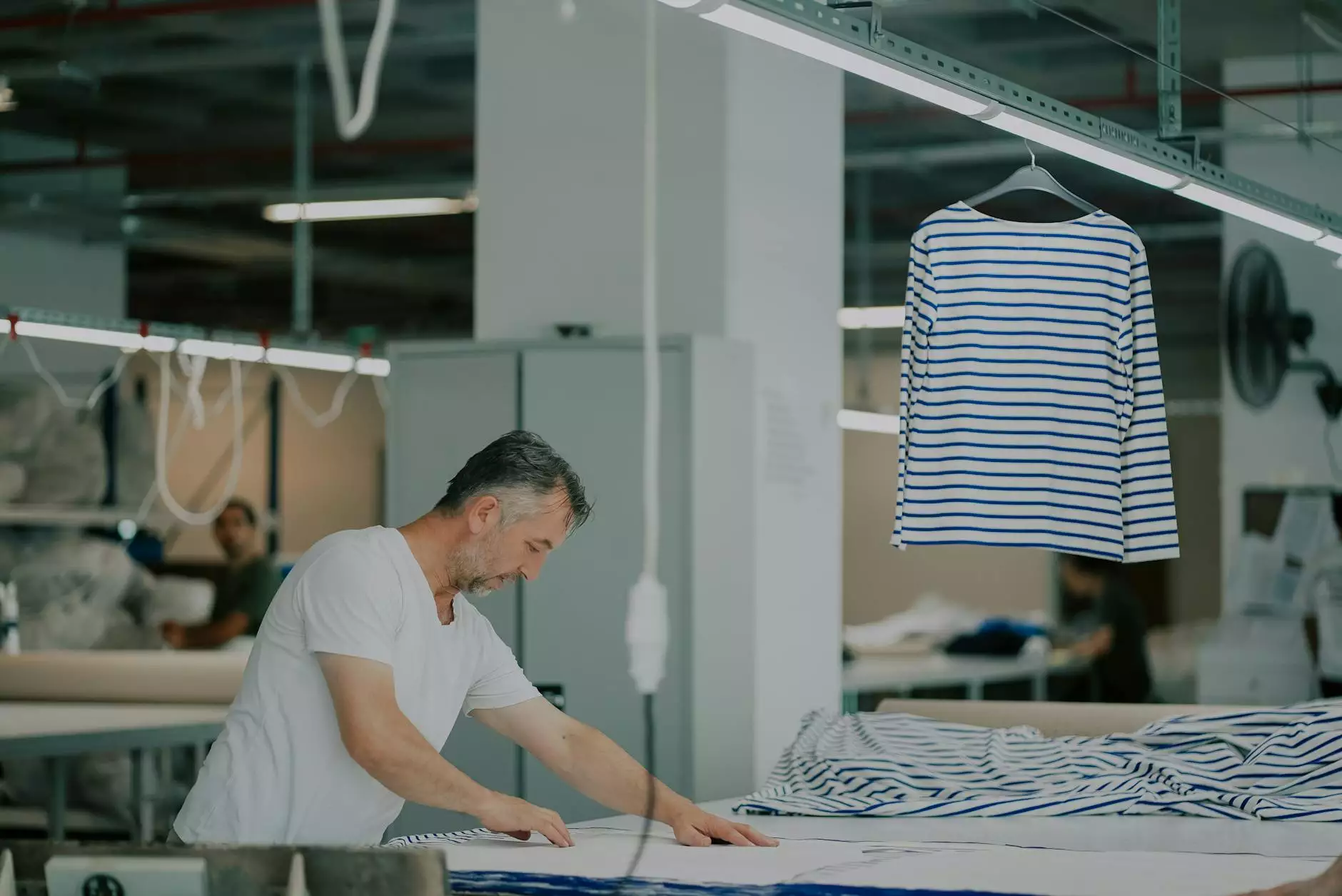
Silicone injection molding machines represent a game-changing technology in the manufacturing landscape. These machines are designed to produce high-quality, intricate silicone products quickly and efficiently. This article delves into how these machines are revolutionizing various industries, particularly in electronics and medical supplies, and how Nolato.com is at the forefront of this transformation.
Understanding Silicone Injection Molding
Silicone injection molding is a process where liquid silicone rubber (LSR) is injected into a mold. The advantages of this method over traditional molding techniques are plentiful:
- High Efficiency: Silicone injection molding machines can produce complex shapes in very short cycles.
- Consistency and Quality: These machines ensure a high level of precision and repeatability, resulting in uniform products.
- Reduced Waste: The process minimizes material waste, making it more environmentally friendly.
The Mechanics of Silicone Injection Molding Machines
The operation of a silicone injection molding machine involves several key components:
- Injection Unit: This unit melts raw silicone rubber and injects it into the mold at high pressure.
- Mold Unit: The mold is crafted to the desired shape of the final product. It can be custom-designed to meet specific requirements.
- Clamping Unit: This unit keeps the mold halves tightly closed during the injection process to prevent leakage.
Understanding these components is crucial for manufacturers looking to optimize their production lines.
Applications in Electronics
In the electronics sector, the demand for silicone components has surged due to their excellent thermal stability, electrical insulation, and resistance to moisture. Here are some applications:
- Keypads and Switches: Silicone rubber is extensively used in the manufacture of flexible keypads and buttons, providing a tactile feel.
- Sealing and Gaskets: Silicone's ability to create airtight seals makes it ideal for protecting sensitive electronic components.
- Encapsulation of Circuits: Silicone can encapsulate electronic circuits, providing protection from environmental hazards.
As manufacturers like Nolato.com continue to innovate, the use of silicone injection molding machines in electronics will only expand, enabling the production of high-performance components.
Revolutionizing Medical Supplies
The medical industry has also significantly benefited from silicone injection molding. Silicone's biocompatibility ensures that products can safely contact the human body. Here’s how these machines are enhancing medical supply production:
- Medical Devices: From catheters to breathing masks, silicone is used for its reliability and safety.
- Laboratory Equipment: Many lab tools and devices rely on silicone due to its chemical resistance.
- Customized Solutions: The flexibility of silicone injection molding allows for the creation of tailored solutions for specific medical needs.
By utilizing silicone injection molding machines, companies can produce these critical components with precision and speed, aligning with the fast-paced demands of the medical industry.
Advantages of Using Silicone Injection Molding Machines
Investing in silicone injection molding technology offers numerous advantages for manufacturers:
- Cost Efficiency: Although the initial investment may be high, the long-term savings through reduced waste and enhanced efficiency make the technology economically viable.
- Quick Turnaround: The rapid cycle times enable manufacturers to respond quickly to market demands.
- Scalability: Manufacturers can easily scale their production up or down based on demand.
Quality Assurance and Standards
To ensure the highest quality products, adherence to industry standards is crucial. Companies like Nolato.com uphold rigorous quality control processes, including:
- ISO Certification: Certification ensures compliance with international quality management standards.
- Continuous Improvement: Regular assessments and updates to processes help maintain product quality.
By implementing these standards, manufacturers can guarantee that their silicone injection molding machine outputs consistently meet or exceed customer expectations.
The Role of Automation in Silicone Injection Molding
Modern silicone injection molding machines are increasingly incorporating automation. This shift brings several benefits:
- Reduced Labor Costs: Automation decreases the reliance on manual labor, lowering overhead costs.
- Increased Production Rates: Automated systems can operate continuously, maximizing output.
- Enhanced Precision: Automation improves the accuracy of the molding process, leading to fewer defects.
As technology advances, the synergy between automation and silicone injection molding machines will drive future innovations in manufacturing.
Future Trends in Silicone Injection Molding
The future of silicone injection molding is promising, driven by trends such as:
- Smart Manufacturing: Integration of IoT devices for real-time monitoring and data analytics.
- Material Advancements: Development of new silicone materials with enhanced properties for specialized applications.
- Sustainability Practices: Increasing emphasis on eco-friendly practices and materials in manufacturing.
These trends will reshape the manufacturing landscape, making it more efficient and aligned with global sustainability goals.
Conclusion: Embracing Innovation
As industries evolve, the adoption of silicone injection molding machines is becoming essential for companies looking to stay competitive. Nolato.com embodies this spirit of innovation, providing cutting-edge solutions for the electronics and medical supplies sectors. By embracing this technology, businesses can enhance their product offerings, improve efficiency, and ultimately drive growth.