Understanding the Role of a Prototype Mold Factory in Modern Manufacturing
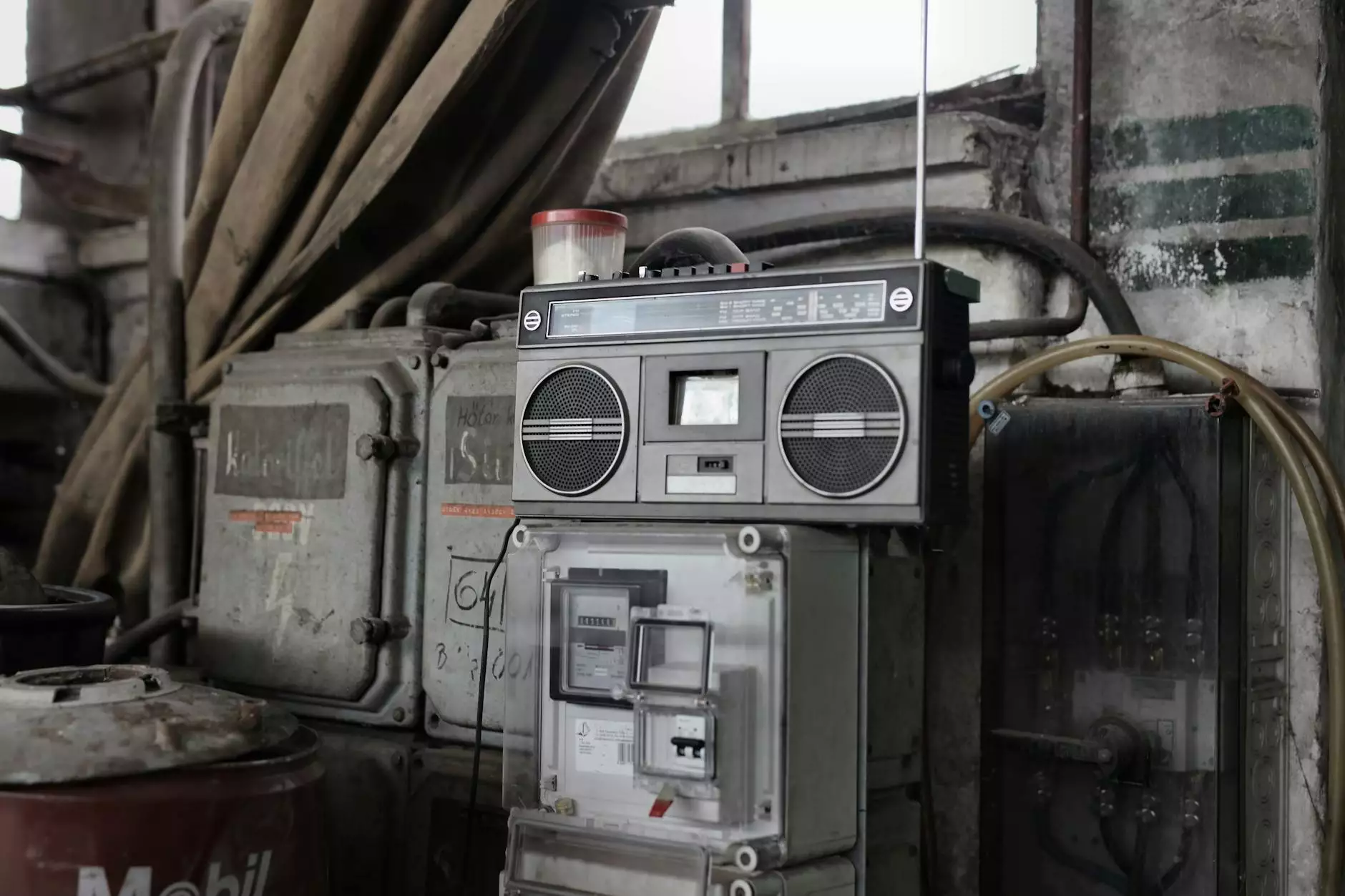
The world of manufacturing has undergone significant transformations over the past decades, driven by innovation, technology, and increasing consumer demand. As companies strive to bring their ideas to life, the importance of a prototype mold factory has soared. This article explores the essential functions, benefits, and methodologies that establish these factories as pivotal players in product development.
The Basics of Prototype Mold Factories
A prototype mold factory specializes in creating molds for experimental or small-scale production runs. These molds serve crucial functions in manufacturing and product design. Here’s a detailed look at what prototype mold factories do:
- Design Consultation: Engineers and designers collaborate to ensure the feasibility of the design.
- Prototype Development: Molds are created to define the shape and form of the product.
- Testing and Validation: Prototype production allows for testing materials and consumer responses.
- Iterative Refinement: Feedback from testing phases leads to adjustments in the mold design, improving the final product.
Why Choose a Prototype Mold Factory?
Investing in a prototype mold factory offers several advantages to businesses, particularly for those looking to innovate and differentiate their products in the marketplace. Here are the key reasons:
1. Accelerated Time to Market
Time is often of the essence in product development. By leveraging the capabilities of a prototype mold factory, businesses can rapidly prototype their ideas, leading to quicker market entry. Here’s how:
- Rapid Prototyping Technologies: Techniques like 3D printing and CNC machining speed up the process.
- Immediate Feedback Loops: Quick iterations based on market realities ensure adaptability.
2. Cost-Effective Solutions
Creating molds in-house can be prohibitively expensive. A specialized prototype mold factory brings scalable solutions that can significantly reduce costs:
- Shared Resources: Factories usually possess advanced machinery that individual companies would struggle to justify for occasional use.
- Expertise on Demand: Skilled personnel handle complex issues, cutting down on labor and training costs.
3. Enhanced Design Quality
Incorporating a professional factory into your product development process leads to superior design quality:
- Precision Engineering: High-end equipment ensures high tolerance levels and accurate designs.
- Material Selection Optimization: Factories have access to a wide range of materials to test for optimal performance.
The Prototype Mold Factory Process
Understanding the process followed by a prototype mold factory is vital for grasping how they contribute to product development. Here’s a comprehensive overview:
1. Design Evaluation
Initially, the design is scrutinized by engineers. This phase focuses on determining whether the design is practical for prototyping. Key considerations include:
- Assessing functionality and manufacturability.
- Checking for any potential design flaws early in the process.
2. Mold Creation
Once the design is approved, the next step is mold fabrication. This step involves:
- CNC Machining: Utilizing Computer Numerical Control milling to achieve high accuracy in mold fabrication.
- 3D Printing: Using additive manufacturing for rapid mold creation, ideal for complex geometries.
3. Prototyping and Testing
Next, the factory produces the first prototype. This phase is critical as it allows
for testing functionality, aesthetics, and market reception. Insights gained from consumer testing can lead to:
- Refinements in Design: Adjustments are made based on feedback to enhance user experience.
- Cost Analysis: Evaluating production costs and modifying materials if necessary.
4. Final Adjustments
After gathering feedback, the final adjustments are made to the molds, leading to a polished product ready for mass production.
Key Considerations When Choosing a Prototype Mold Factory
Not all prototype mold factories are created equal. Here are crucial factors to consider when selecting a factory partner:
1. Expertise and Experience
A factory with a rich history in mold-making and a diverse portfolio of successful projects will provide confidence in their capabilities.
2. Technological Advancements
Innovative factories leverage cutting-edge technologies, ensuring efficient and precise production processes. Look for:
- Advanced CNC machines.
- State-of-the-art 3D printing capabilities.
3. Customization Options
Ensure the factory offers tailored solutions suited to your specific needs. Flexibility in design changes and manufacturing processes is vital for successful outcomes.
4. Quality Assurance Measures
The best factories will implement rigorous quality checks at every stage of the production process, ensuring that the final product meets high standards.
Conclusion: The Future of Production with Prototype Mold Factories
In conclusion, a prototype mold factory plays a pivotal role in the modern manufacturing landscape. They not only facilitate rapid product development but also assure quality and optimization, allowing businesses to bring innovative products to market with confidence. As industries continue to evolve and adapt to new challenges, the collaboration between businesses and prototype mold factories will undoubtedly flourish, paving the way for groundbreaking products that meet the demands of consumers both today and in the future.
As you look to enhance your product development capabilities, consider the advantages of working with a reputable prototype mold factory. By aligning your business with expert partners like Deep Mould, you are ensuring that your ideas are transformed into successful physical products, with optimal efficiency and quality.